Máy hàn điện xỉ áp lực
Máy hàn điện xỉ áp lực dùng để hàn nối đối đầu cốt thép tại hiện trường các công trình xây dựng và trong xưởng sản xuất.
Chu trình hàn nối đối đầu theo phương pháp hàn điện xỉ áp lực diễn ra nhanh chóng và đơn giản.
• Vị trí để hàn đối đầu hai cây thép được thiết kế như sau: hai đoạn cốt thép cần nối được định vị thẳng tâm và đối đầu nhau thông qua má kẹp trên và dưới của bộ đồ gá hàn. Đồ gá hàn được thiết kế đặc biệt để có thể điều chỉnh được khoảng cách giữa 2 cây thép, đồng thời tạo ra lực ép khi kết thúc quá trình hàn.
• Cây thép phía dưới được nối với cực (-) của máy hàn thông qua 1 kìm hàn, cây thép phía trên được nối với cực (+) của máy hàn thông qua 01 kìm hàn khác.
• Xung quanh mối nối được bao bọc bằng thuốc hàn nhờ một phễu thuốc. Với mô hình như vậy, cây thép phía dưới sẽ là vật hàn, cây thép phía trên là điện cực hàn xỉ. Thuốc dưới tác dụng của hồ quang sẽ bị nóng chảy và tạo thành xỉ lỏng, đồng thời lượng thuốc hàn xung quanh không bị nóng chảy sẽ đóng vai trò như các má trượt bao bọc xung quanh để tạo bể xỉ.
• Ở vị trí ban đầu, hai cây thép tiếp xúc với nhau, sau đó nhờ cam điều chỉnh vị trí của đồ gá hàn, hai đầu cây thép tách nhau ra. Lúc này dưới tác dụng của điện áp hàn (40–42V), giữa hai đầu cây thép xảy ra hiện tượng phóng hồ quang ở nhiệt độ rất cao sẽ làm nóng chảy toàn bộ bề mặt tiết diện ngang của hai đầu cây thép đồng thời cũng làm nóng chảy thuốc hàn xung quanh. Khi lượng thuốc hàn nóng chảy đủ lớn để tạo thành bể xỉ, đồ gá hàn sẽ đẩy cây thép phía trên về phía bể xỉ. Lúc này, hồ quang sẽ tắt, điện áp hàn giảm xuống 22-25V, dòng điện sẽ truyền từ cây thép phía trên xuống cây thép phía dưới thông quan bể xỉ, dòng điện này sẽ đốt nóng bể xỉ, duy trì nó ở nhiệt độ cao và có tính dẫn điện cao. Nhiệt độ bể xỉ cao hơn nhiệt độ nóng chảy của cây thép. Do vậy, các cây thép sẽ tiếp tục bị nung chảy ở nhiệt độ cao của bể xỉ. Khi lượng kim loại nóng chảy đủ để liên kết tạo thành mối hàn, ngay lập tức, đồ gá hàn sẽ thực hiện chu trình ép hai đầu cây thép đã nóng chảy với nhau để tạo thành mối hàn có tiết diện ngang lớn hơn tiết diện của cây thép.
• Mối hàn lúc này được bao bọc bởi bể xỉ có nhiệt độ cao, lại không có quá trình làm mát của các má trượt, do vậy sau khi hàn cần giữ mối hàn nguyên trạng trong thời gian nhất định để làm nguội và đóng cứng bể xỉ nhằm làm đông đặc và bảo vệ kim loại hàn.
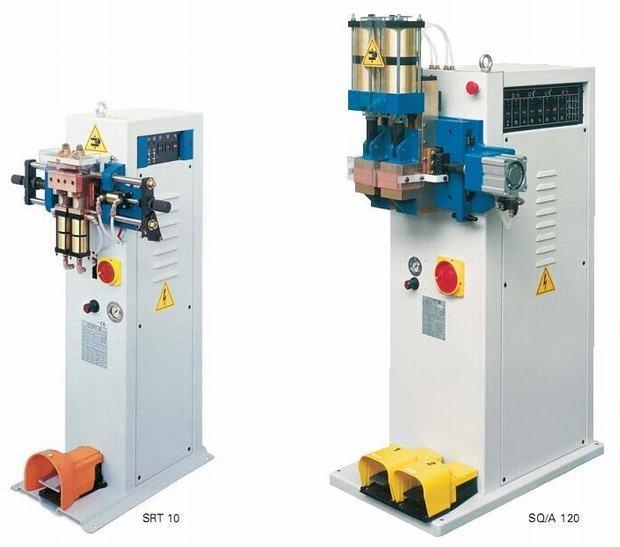
Thông số kỹ thuật:
• Đường kính cốt thép nối quy định: 14-36 mm.
• Loại cốt thép: thép gai, thép tròn.
• Công suất: 25kVA - 630A, năng suất: 100 mối hàn/ ca.
Ưu điểm:
Trang thiết bị gọn nhẹ, dễ sử dụng, thuận lợi cho việc thao tác tại nhiều vị trí: thẳng đứng, nằm ngang, nằm nghiêng, trong không gian chật hẹp, thuận lợi khi hàn những dầm hoặc trụ thép có nhiều cây cốt thép.
• Thời gian hàn ngắn nên năng suất lao động cao.
• Lực ép hai đầu cốt thép không cần quá lớn so với hàn đối đầu tiếp xúc, do vậy đồ gá hàn gọn nhẹ, rẻ tiền.
• Dòng điện hàn thấp nên biến thế hàn nhỏ, dễ chế tạo hơn nhiều so với hàn điện tiếp xúc.
• Chất lượng mối hàn cao (do được bảo vệ trong lớp thuốc hàn nóng chảy), không rỗ, không ngậm xỉ, kim loại mối hàn đồng đều với kim loại cơ bản do không cần kim loại bù. Mối hàn được ủ bởi lớp thuốc nên không bị hiện tượng nứt hoặc giảm cơ tính ở vùng ảnh hưởng nhiệt.
• Vì cốt thép được hàn đồng tâm nên khả năng chịu lực kéo, nén của cây thép tăng. Tiết diện mối hàn tại mối nối lớn hơn tiết diện ngang của cây thép nên cơ tính tại mối hàn cũng tăng, khả năng liên kết với bê tông tốt hơn.
Lò đốt chất thải nguy hại
Lò gồm những bộ phận chính như sau:
1. Buồng đốt sơ cấp: để hóa khí các chất nguy hại, sử dụng công nghệ nhiệt phân hóa khí chất thải, được duy trì ở nhiệt độ 650-850o C.
2. Buồng đốt thứ cấp: đốt cháy khói thải đi từ buồng sơ cấp sang, được duy trì nhiệt độ từ 1.050-1.300oC.
3. Buồng lưu nhiệt: khí thải đi từ buồng đốt thứ cấp được đi vào buồng lưu nhiệt và do được bảo ôn nên tiếp tục được đốt cháy, kéo dài thời gian lưu cháy.
4. Bộ phận làm mát khí thải và thu hồi nhiệt: tại đây thực hiện quá trình trao đổi nhiệt giữa khói và nước để hạ nhiệt độ khói thải xuống 3000C trước khi đi vào tháp xử lý khói.
5. Hệ thống xử lý khí thải và ống khói: được thiết kế tổ hợp giữa hai thiết bị là cyclon tách bụi và tháp xử lý ướt. Khói thải sau khi xử lý đi lên ống khói thải ra môi trường.
6. Hệ thống cấp khí
7. Tủ điều khiển: điều khiển hoạt động của lò và các đồng hồ báo nhiệt độ lò sơ cấp, nhiệt độ lò thứ cấp. Tủ điều khiển còn có chức năng báo động, bảo vệ tự ngắt khi sốc nhiệt hoặc bị mất pha.
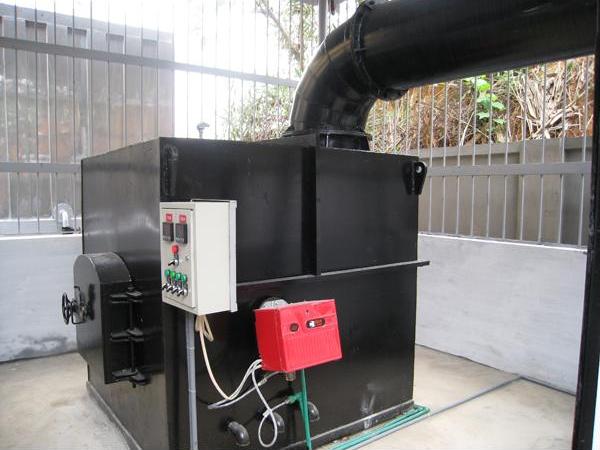
Thông số kỹ thuật:
• Công suất: 80kg/giờ, nhiên liệu: dầu DO.
• Kích thước cơ bản: 1800 x 1800 x 3350 mm; thể tích buồng đốt rác: 2,2 m3; thể tích buồng đốt khói: 0,9 m3; thể tích buồng hạ nhiệt: 0,4 m3.
• Vật liệu buồng đốt: bê tông dày 250 mm, chịu nhiệt 1.600oC; lớp cách nhiệt dày: 50 mm.
• Vật liệu buồng hạ nhiệt: làm bằng INOX SUS lớp bê tông chịu nhiệt dày 100 mm.
• Vỏ lò: thép tấm 6 mm, khung thép chịu lực, sơn chịu nhiệt đến 300oC.
• Thu hồi nhiệt để sấy khô rác, giảm tiêu hao dầu.
• Chế độ làm việc liên tục 24/24.
Ưu điểm:
• Sử dụng công nghệ khí hóa chất thải, tạo cho lò luôn luôn có áp suất âm.
• Tiết kiệm nhiên liệu: do buồng lò dày lại có lớp bê tông cách nhiệt nên không bị mất mát nhiệt.
• Vận hành đơn giản, không đòi hỏi nhiều nhân công do được tự động hóa.
• Do sử dụng công nghệ cấp khí tự động nên chỉ cần một quạt cấp khí rất nhỏ để bổ sung không khí, không phải dùng quạt cấp khí cho buồng sơ cấp, buồng thứ cấp.
• Hệ thống xử lý sử dụng cyclon áp lực và phun sương có khả năng loại bỏ triệt để bụi và khí axit, …
• Khí thải thoát ra đạt tiêu chuẩn môi trường TCVN 6560:2005, QCQG 02-2008.
Dây chuyền tự động xử lý lông vũ và sản xuất đạm hấp thu từ lông vũ phế thải
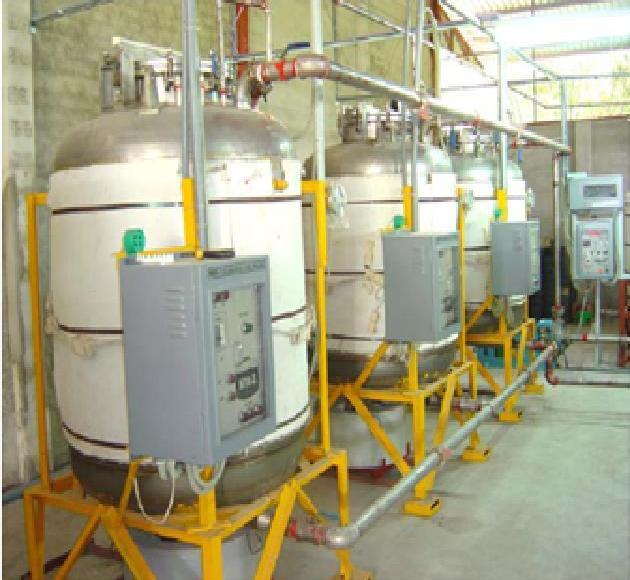
Hệ thống này cho phép tạo nguồn đạm chăn nuôi từ lông vũ phế thải với giá thành rẻ, chất lượng cao để thay thế nguồn đạm bột cá không ổn định về số lượng và chất lượng, góp phần đẩy mạnh chăn nuôi và mở rộng sản phẩm đạm cho các lĩnh vực khác. Hệ thống sản xuất không có chất thải, góp phần xử lý rác thải môi trường, làm sạch môi trường.
Quy trình công nghệ:
1. Nghiền –xay lông vũ phế thải thành bột có kích khoảng 4 – 6 mm.
2. Xử lý sơ bộ (ngâm, khuấy đảo) bột lông vũ bằng dung dịch xút loãng (NaOH 0,8%) trong 48 giờ thu được hỗn hợp 1.
3. Đun sôi hỗn hợp 1.
4. Xử lý chính hỗn hợp 1 ở áp suất 2-3 at trong thời gian 3 giờ thu được dung dịch đạm lỏng.
5. Trung hòa dung dịch đạm lỏng bằng axit HCL có nồng độ 5N, thu được dung dịch đạm lỏng 2 có nồng độ đạm 10-15%, độ pH=7.
6. Cô đặc dung dịch đạm bằng cách phun ngược chiều với hơi nóng ở nhiệt độ 1000C trong 3 giờ, tiếp tục cô đặc để tạo dung dịch sệt.
7. Phối trộn dung dịch sệt với phụ gia cao lanh theo tỉ vệ 30-50% so với nguyên liệu ban đầu thu được bột ướt. Tỷ lệ phụ gia tùy thuộc hàm lượng đạm cần có.
8. Sấy khô bột ướt bằng khí nóng ở nhiệt độ 1000C trong 5 giờ thu được bột khô.
9. Xay bột khô thành bột mịn.
10. Đóng gói thành phẩm. Sản phẩm cuối cùng thu được dạng bột mịn, màu hổ phách, có mùi đặc trưng keratine, hàm lượng đạm 50-70%.
Ưu điểm CN/TB:
• Dây chuyền hoàn toàn tự động, dựa trên các PLC điều khiển.
• Xử lý lông vũ với hiệu suất 100%, không có chất thải rắn.
• Giá thành sản phẩm đạm rẻ so với sản phẩm đạm tương đương. (chỉ bằng 50-60% bột cá)
• Không có độc tố, phù hợp sử dụng cho chăn nuôi.
• Độ vô trùng cao, bảo quản lâu dài.
STINFO số 5/2013